TEAM D3 DRIVES TRANSFORMATION AND CONTINUOUS IMPROVEMENT IN THE MANUFACTURING, AECO AND PROCESS & POWER INDUSTRIES.
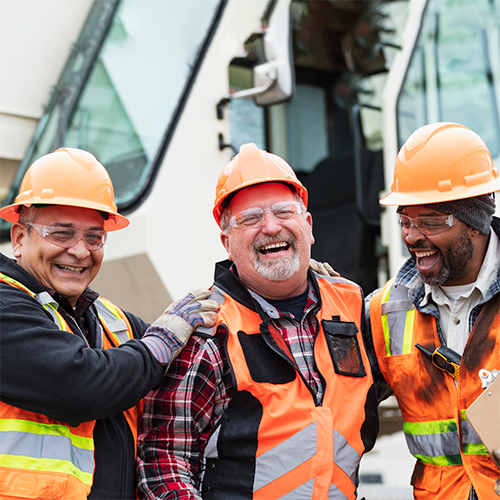
WHY SHOULD IT BE A KEY PART OF YOUR TEAM'S STRATEGY?
IMPROVED ORGANIZATIONAL EFFECTIVENESS:
Continuous improvement helps to identify inefficiencies in your team's processes, allowing you to streamline operations and save time and resources.
INCREASED ACCOUNTABILITY:
Teams must take ownership of their actions and identify areas for improvement to foster continuous improvement & accountability. Clear goals, feedback, and roles are key.
BOOSTED TEAM MENTALITY:
When your team is constantly improving, they feel a sense of accomplishment and pride in their work. This leads to increased job satisfaction and higher employee retention rates.
ENHANCED SKILL SETS:
Continuous improvement allows your team to identify and eliminate roadblocks that hinder productivity, leading to increased output and faster completion times.
THE CONTINUOUS IMPROVEMENT PROCESS:
- IDENTIFY THE AREA FOR IMPROVEMENT
- ANALYZE THE CURRENT PROCESS
- SET GOALS AND OBJECTIVES
- DEVELOP A PLAN
- IMPLEMENT THE PLAN
- MONITOR AND EVALUATE
- ADJUST AND REFINE
- COMMUNICATE THE RESULTS
- REPEAT THE PROCESS
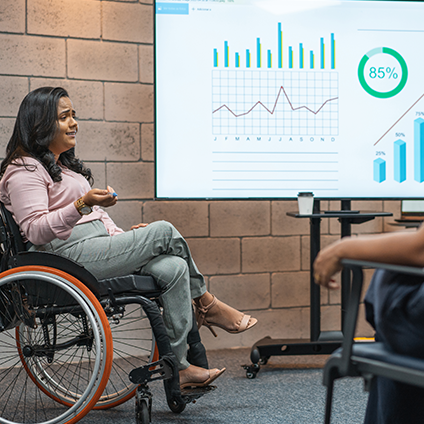
Schedule a Consultation
Schedule a one-on-one consultation with our team of experts helping organizations like yours achieve their goals through the power of continuous improvement.
Subscribe to our Lean Enterprise Blog
You'll receive regular updates straight to your inbox, ensuring that you never miss a post!
PS: We are doing a year long blog series on continuous improvement too!